Week 5 - Computer-Controlled Machining
Making Something Big
The project this week was to make something big using the Shopbots. The main limitation for this assignment was that the Shopbot bed in Harvard can only fit up to 4x4 feeet. The material we were given was OBE wood, which is a workable but not the highest quality wood.
My idea for this week was to make a side table where I could add a small light. I've recently developed a habit of watching youtube videos in my bed before I sleep, but I am often too lazy to turn off the light after. As such, I end up turning off the light before I lay in bed and watching the youtube videos in the dark. Having a small light right beside my bed which I can turn off without getting up would be perfect for my lazy self, and a side table to put my small lamp would be ideal.
Almost everything wrong that could go wrong happened. First, Fusion360 kept on messing up. Whenever I would try to draw a line, it would suddenly switch to a different plane or not allow me to draw. After about 10 clicks, it would finally let me a line, but then suddenly random lines would pop up and Fusion would inform me that I have too many restraints. Problems like this led to me taking several hours to draw a mere side table. Then, the next problem was with exporting. I tried saving the entire figure as a DXF, but Daniel Davis told me that I need each individual figure flat on a plane. So, I then tried saving each individual piece as a DXF and converting to PDF as it worked for my classmates. Not for me. The figures would not export flat on a plane. I even tried rotating the sketches within Fusion, but the PDFs would always be of a figure at an angle. After an hour of asking people and struggling, I ended up just redrawing the figures on VCarve Pro. At last, I had figures I could print!
I then began to actually make something big. We first cut test pieces to see if the pieces would fit together well. The pieces press-fit well together, so I thought I saw a light at the end of the tunnel.
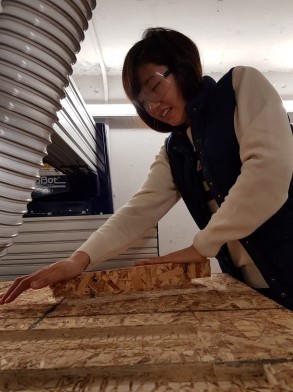
The light disappeared pretty quickly. The Shopbot actually stopped working in the middle of my cut, asking us to reset and saying that it could not find the location. We reset and re-zeroed the z, thinking that the machine remembered x and y position. It turns out that it did not. Consequently, we decided that we could re-zero based on the location of a corner of the test cut piece. However, the reset warning kept on popping up and eventually, we couldn't move the spindle without triggering a warning. We tried turning the entire machine on and off, computer on and off, but to no avail. As of now, the best big thing I have is my test piece.
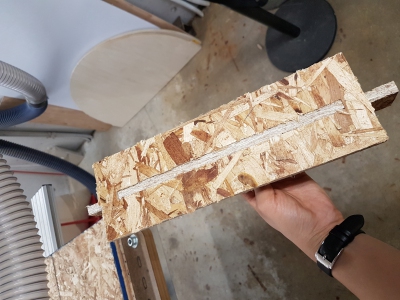
The next day, I received the exciting news that the Shopbot was working again. I was able to see the light again. I went downstairs to the shop, and with a functioning Shopbot, in 12 minutes I had all the pieces for my side table. With some sanding and press-fitting, I had my first handmade furniture!
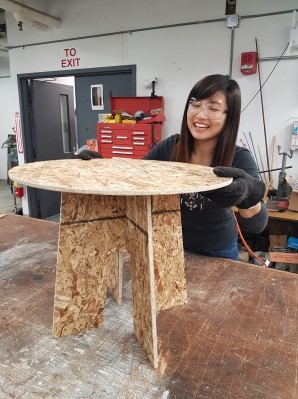
Much thanks to Daniel Davis for being patient as I fumbled with exporting and cutting.